Corrosion in cargo and water ballast tanks presents a significant challenge. DNV analyses reveal that corrosion is the most common cause of hull findings, and our surveyors often discover coatings breaking down much earlier than anticipated. Exposure of the ship structure to high temperatures may be a possible reason. This technical news explores the topic in more detail.
Corrosion in water ballast and cargo tanks – DNV observations
The actual corrosion rate in ballast and cargo tanks may differ from the assumptions in the rules and the embedded corrosion models. DNV survey data reveals a significant rise in corrosion findings in water ballast and cargo tanks in oil tankers and bulk carriers at the third renewal survey, with a peak at the fourth renewal (Figure 1). That means that for some vessels, the useful life of the effective coating protection may only be about two-thirds of the requirement of the Performance Standard for Protective Coatings (PSPC).
DNV material experts emphasize that the deterioration process is not linear, nor are the consequences. Once the protective coating begins to break down, corrosion advances swiftly, leading to issues such as pitting, edge or grooving corrosion. An analysis of the DNV survey data indicates that many findings were recorded in locations suspected to be exposed to elevated temperatures, where the corrosion rate and spreading were even more advanced.
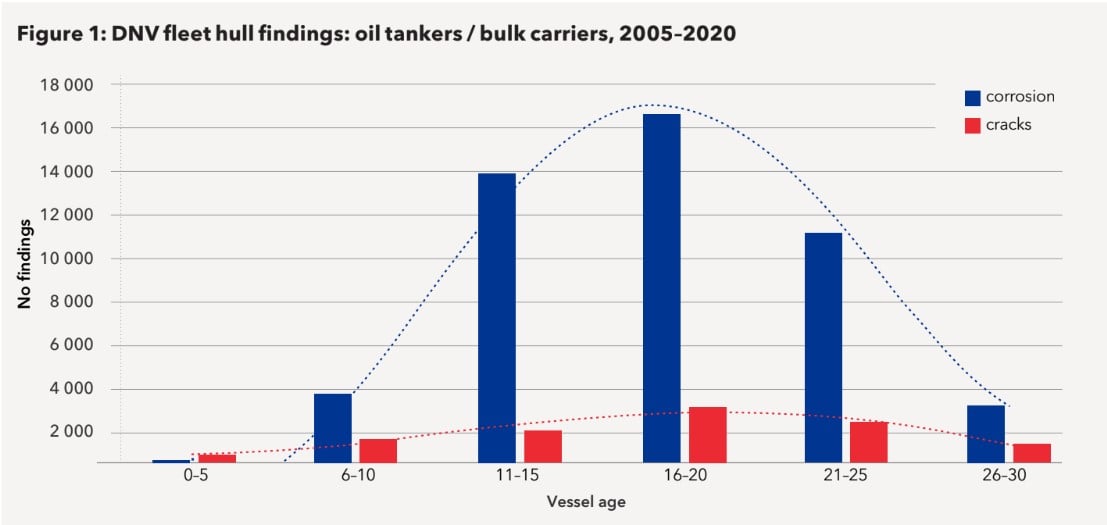
Causes of coating deterioration
The causes of coating deterioration and failure are complex, often involving multiple factors simultaneously. Corrosion depends on ambient conditions such as salinity, acidity, humidity, temperature, time of exposure, and coating condition. The degradation rates are highly non-linear and time-dependent and vary significantly.
Coating makers claim that most coating failures result from poor surface pre-treatment and/or an inadequate coating application. Conversely, ship insurance companies and charterers argue that most coating failures stem from incorrect specifications (poor design or quality) and operational conditions that exceed design limits. Examples include higher cargo storage temperatures for extended periods, incorrect cleaning procedures, and mechanical damages during cargo and ballast operations.
Influence of temperature on corrosion
Among all factors affecting the corrosion rate, exposure to high temperatures is often overlooked. Simulation models based on actual test data performed by DNV show that the corrosion rate of bare carbon steel increases by approximately 30% for every 10oC increase in temperature (Figure 2). Coated steel will also be impacted by temperature, as it accelerates the ageing of the coating, leading to early signs of local coating breakdown at hard points, welds and other vulnerable areas.
Ballast tanks adjacent to heated cargo/fuel tanks are a prime example. DNV’s recent surveys reveal that increased steel corrosion was recorded even though the tank coating had been rated “Good” in the previous class survey.
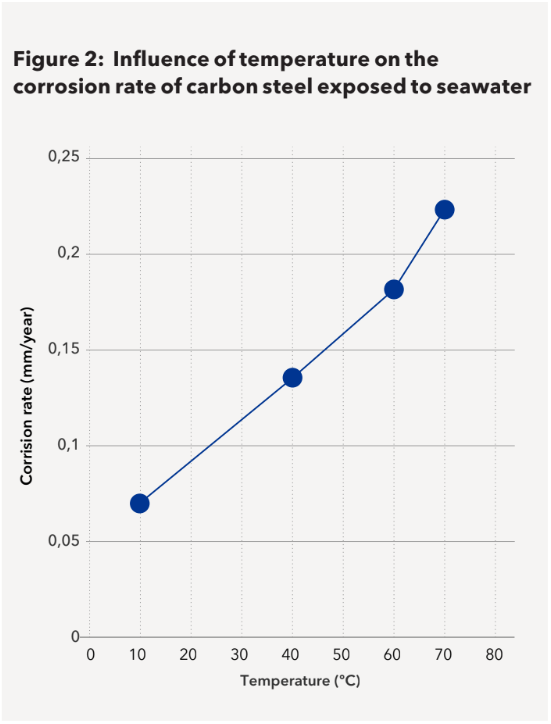
Effects of corrosion damage
Loss of structural integrity: Corrosion leads to thickness reductions at both the local and general level. While local corrosion such as pitting or grooving may not represent an overall safety problem, it can facilitate the formations of cracks, holes or surface anomalies, leading to leakage into ballast tanks, which in turn can cause environmental damage, or contamination of cargo with ballast water (Picture 1, right). A “domino” effect may also occur, whereby steel/welding wastage and cracking due to local corrosion in multiple members lead to an overload of adjacent members. This can result in their failure under short-term exposure to loads higher than designed, potentially causing serious overall structural failure (Picture 1, left).
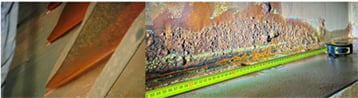
Picture 1: Corrosion leading to “domino” cracking (left), and grooving leading to cracking and leakage (right)
Maintenance/operation cost: Corrosion increases maintenance and repair cost if not addressed promptly. Misjudging the coating condition in areas with an accelerated corrosion rate may necessitate steel renewals even between the scheduled class survey periods, impacting off-hire cost or breaches of contract (Picture 2).
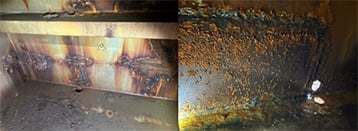
Picture 2: Coating condition after two years, with repairs involving a poor coating application
Recommendations
Maintenance of coating: Maintaining the original protective coating of the interior surfaces of ballast tanks is one of the most effective methods to prevent corrosion. Repairs should be performed by qualified personnel adhering to the coating maker’s instructions. If not, the risk of early coating damages after repairs is very probable.
Regular coating inspections: Implementing a regular inspection and maintenance scheme is essential to identify and address corrosion issues before they become severe.
DNV class expertise: Involving DNV early on for an assessment of the coating condition helps to be aware of the tank status. DNV provides a custom hull survey plan to closely monitor the condition of tanks reported with corrosion damage or a coating condition rated “Fair” or “Poor”. Targeted surveys, in addition to the periodical surveys, can be introduced to include the reported tanks in the upcoming survey’s scope.
The DNV-CG-0288 (Ref. 2) provides comprehensive guide- lines for the corrosion protection of ships, outlining methods, technical requirements, principles and acceptance criteria related to corrosion protection.
The DNV class notation COAT-PSPC ensures that all stages of coating in cargo and ballast tanks are checked and verified the construction at the yard.
References
- DNV rules for ships, Pt. 7 (visit DNV Rules and Standards Explorer: see https://store.veracity.com/rules-and-standards-explorer)
- DNV-CG-0288 “Corrosion protection of ships”
- IMO Resolution MSC.215(82) “Performance standard for protective coatings for dedicated seawater ballast tanks in all types of ships and double-side skin spaces of bulk carriers”
- DNV-CP-0429 “Corrosion resistant steels for cargo oil tanks”
Contact
- For customers:
DATE – Direct Access to Technical Experts via My Services on Veracity. - Otherwise:
Use our office locator to find the nearest DNV office.